Overview
At our core, CF Industries is a manufacturer of ammonia. Ammonia is most often used as a fertilizer itself or is upgraded into other nitrogen fertilizers, such as granular urea and urea ammonium nitrate solution.
Like other producers of ammonia, we use the Haber Bosch process, considered one of the most impactful innovations of the 20th century, which synthesizes nitrogen from the air with hydrogen. In addition to Green Revolution seed enhancements and farming practice improvements, the growing use of nitrogen and other fertilizers dramatically improved food production in the second half of the 1900s. The annual rate of people dying due to famine globally per decade declined nearly 99% from the 1960s to the 2010s.
As such, our team and the products we make play a direct and vast role in ensuring the world’s population has enough food to eat. Our fertilizer also limits the destruction of forests, which play a role in offsetting greenhouse gas emissions by sequestering, or naturally capturing, carbon dioxide (CO2). Ammonia and its upgraded products are also used for emissions control and other industrial processes.
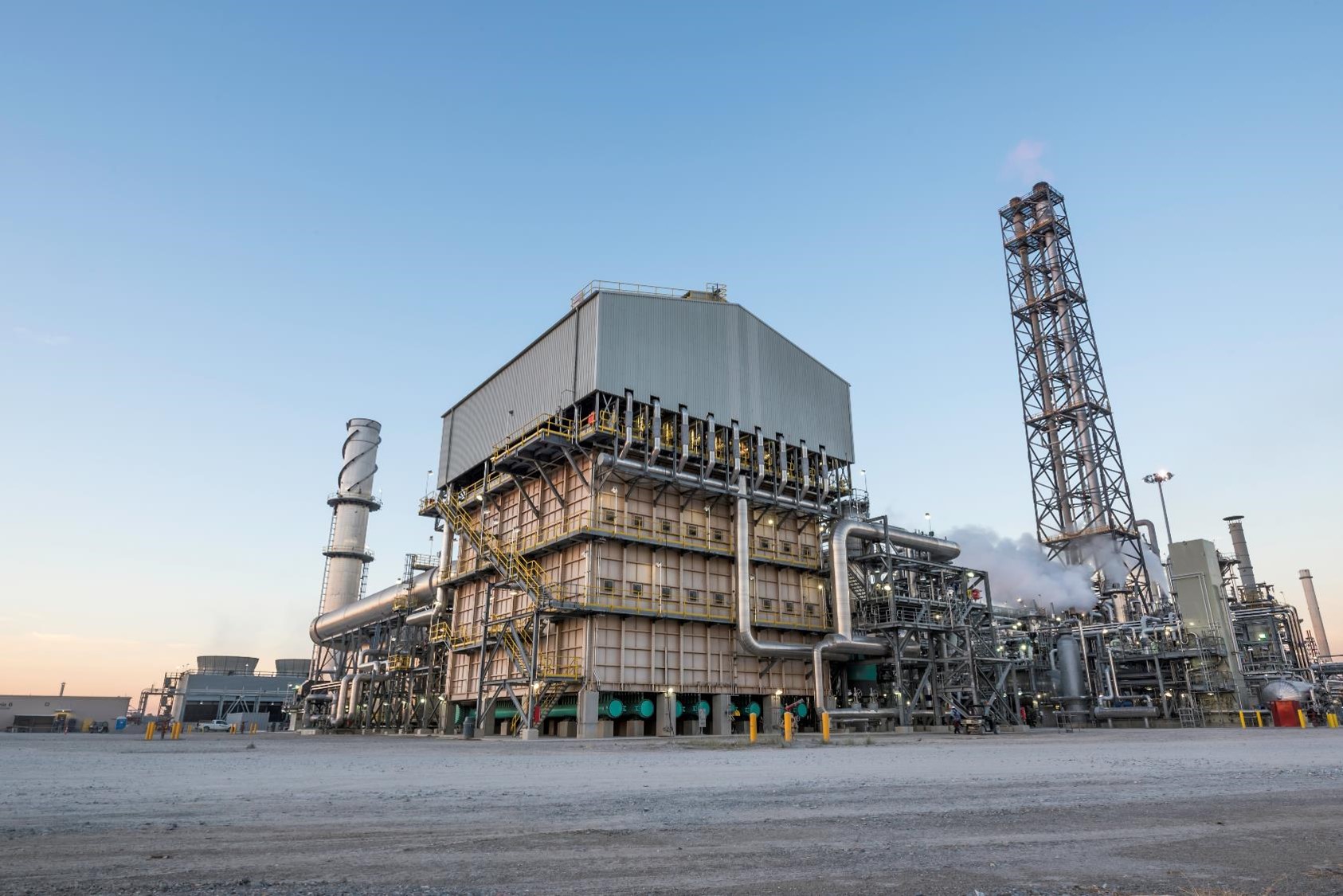
Donaldsonville Complex Ammonia 6
The Donaldsonville Complex's Ammonia 6 plant is the largest ammonia plant in the world. The plant came online in 2016.
Haber-Bosch Process
Haber-Bosch process, also called Haber ammonia process, or synthetic ammonia process, method of directly synthesizing ammonia from hydrogen and nitrogen, developed by the German physical chemist Fritz Haber. He received the Nobel Prize for Chemistry in 1918 for this method, which made the manufacture of ammonia economically feasible. The method was translated into a large-scale process using a catalyst and high-pressure methods by Carl Bosch, an industrial chemist who won a Nobel Prize in 1931 jointly with Friedrich Bergius for high-pressure studies.
Haber-Bosch was the first industrial chemical process to use high pressure for a chemical reaction. It directly combines nitrogen from the air with hydrogen under extremely high pressures and moderately high temperatures. A catalyst made mostly from iron enables the reaction to be carried out at a lower temperature than would otherwise be practicable, while the removal of ammonia from the batch as soon as it is formed ensures that an equilibrium favouring product formation is maintained. The lower the temperature and the higher the pressure used, the greater the proportion of ammonia yielded in the mixture. For commercial production, the reaction is carried out at pressures ranging from 200 to 400 atmospheres and at temperatures ranging from 400° to 650° C (750° to 1200° F). The Haber-Bosch process is the most economical for the fixation of nitrogen and with modifications continues in use as one of the basic processes of the chemical industry in the world.
Source: Brittanica
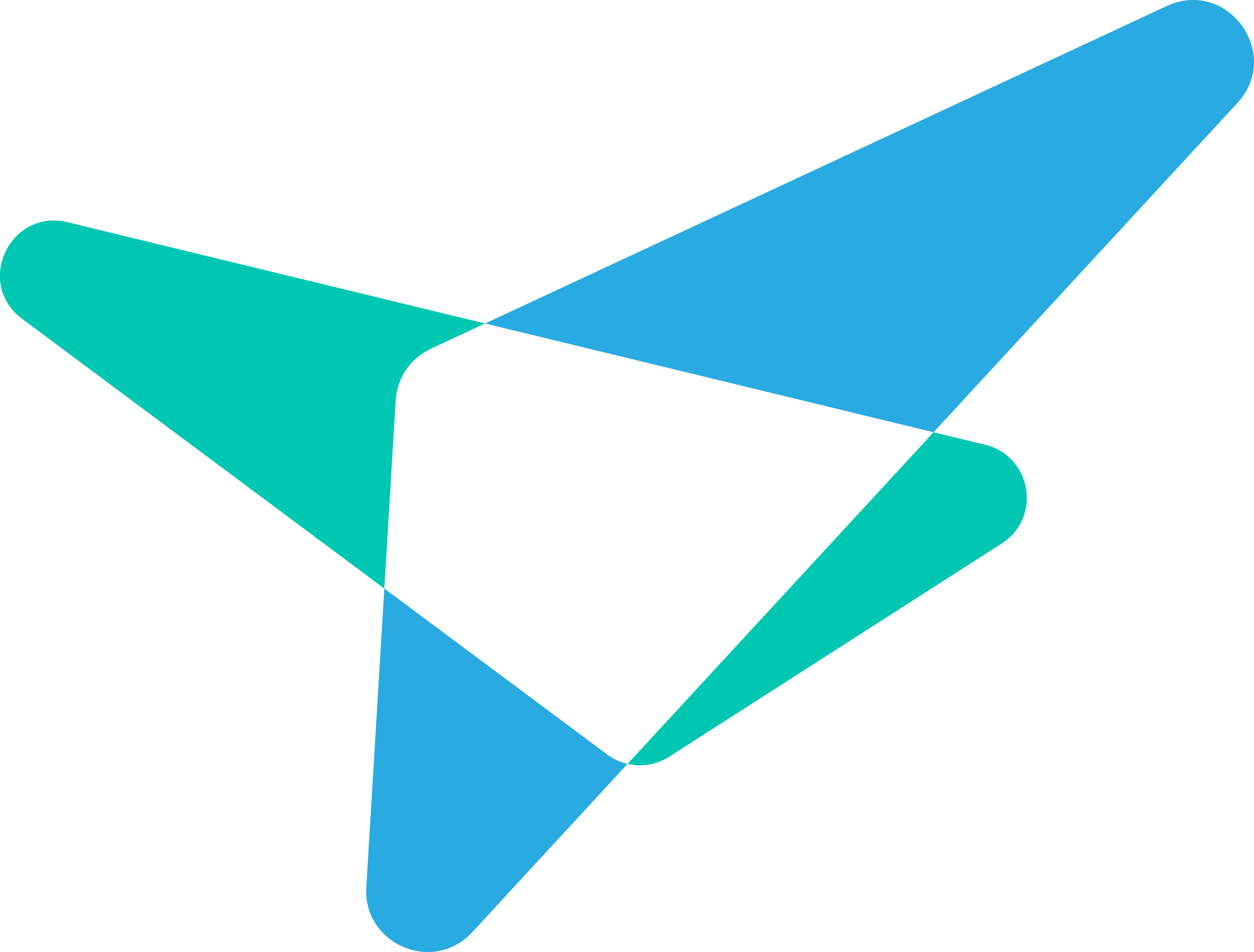
CF Industries Average Annual Gross Ammonia Capacity By Location
- Donaldsonville (Louisiana) - 4,335,000 tons (largest ammonia production complex in the world)
- Medicine Hat (Alberta) - 1,230,000 tons (largest ammonia production complex in Canada)
- Port Neal (Iowa) - 1,230,000 tons
- Verdigris (Oklahoma) - 1,210,000 tons
- Billingham (UK) - 590,000 tons
- Yazoo City (Mississippi) - 570,000 tons
- Courtright (Ontario) - 500,000 tons
- Woodward (Oklahoma) - 480,000 tons
- Point Lisas* (Trinidad) - 360,000 tons
*Joint venture